Advanced Radon Technologies, Inc. - Commercial
Advanced Radon Technologies with 45 years of HVAC mechanical engineering experience and a patented diagnostic testing machine ART specializes in designing and installing large radon mitigation systems in unique and complex commercial buildings. ART understands the complexities of commercial HVAC systems the controls and the interaction of those systems and radon. ART uses commercial techniques and commercial systems/fans unlike most radon companies that utilize residential radon system for commercial structures. Art also installs Vapor Intrusion systems in commercial structures. ART's Patented diagnostic testing machine and years of experience in large radon mitigation systems has made ART a world leader in the design and installation of large commercial Vapor Intrusion systems.
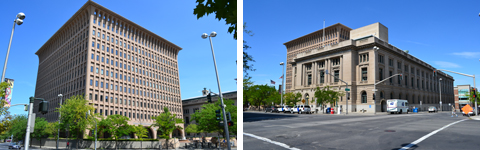
ART installed the radon mitigation system in the US Post office and Federal courthouse in 1995. It is the largest and most complex radon mitigation system in world. It required several corrections to the complicated mechanical system as the Sub basement is 22' below grade and under the parking garage making the design of the radon system challenging and dependent on repairing the HVAC system. Please see the Case Studies page for more detail on this building and radon system.
Advanced Radon Technologies is actively seeking commercial radon mitigation projects all over the United States as we have already completed several significant projects all over the Pacific Northwest Just a few examples of significant projects we’ve done include the McChord AirForce Base Mission Support Center, U.S. Federal Courthouse and Post Office, Portland Public School District, several unique retirement centers and hundreds of apartment complexes.
Our radon experts use a number of standard procedures for sub-slab diagnostics, utilizing advanced tools that successfully remediate and remove radon. Our core drill is used to create the evacuation holes, completing each 5” diameter hole in less than 5 minutes. This allows for a cleaner installation of the mitigation system. It is also can be used to drill large holes through thick concrete floor and wall up to 14" diameter. ART as built a heavy duty evacuation vacuums remove soil from each hole and draw it into a dump canister. Finally, ART's Patented diagnostic testing machine is used to stimulate the airflow and suction rates of each floor penetration. This is much more complicated then using standard residential radon systems that is often employed by other mitigations companies. Our diagnostic tester provides an accurate readout of air volume and static pressure to be used to select the most appropriate commercial grade fan.
Advanced Radon Technologies has a 100% success rate for removing radon in commercial applications and doing things right the first time. Contact us to learn more about what we do.
If you’re interested in learning more, click on the blue bars to view examples of our buildings and commercial radon systems and fans.

Case Studies
One of the best ways to see how the services Advanced Radon Technologies provides works is to look at clients’ entire process from start to finish. We have documented a number of case studies to present various environments, note how radon gas and other toxins affected the environment, how the chemicals accumulated, and how we were able to eradicate them. If you’re interested in learning more, click on the blue bars to view case studies for just a few of many Spokane area properties we’ve worked with.

McChord Air Force Base Mission Support Center
The McChord Air Force Mission Support Center building has 100,000 sqft of basement and crawlspace and is over 900 feet long. Portions of the basement slab were removed and re-poured with seismic upgrades, while other portions remained intact. Asbestos was found in the crawlspace so special measures were required.
The original specifications for this building called for a minimum of 50 and as many as 100, residential type systems to be installed (like the one seen here, installed by a previous contractor) around the exterior of the building.
The drop ceiling throughout the entire building is being utilized as the cold air return. With the porous soil and high air volume, this would make a large number of residential type systems necessary around the exterior of the building. Our system is incorporated into the remodeling work and will be almost completely hidden when the project is completed.
The pictures that follow show the unique aspects of installing a commercial radon system in this type of structure.
1¼" steel rebar and 5/8" steel rebar were added to the footings for seismic upgrade before the concrete was poured. The 1¼" rebar was tied to the existing foundation. With the large amount of rebar in the footings, it is not feasible to go through the footings with the radon pipe.
This footing is 10' across and 6' deep. The soil underneath the footings is highly compacted. The footings in this building divide the foundation into sections. Each section must be depressurized separately.
A 12" thick sheer wall will sit on top of the footing and extend through all four floors of the building to the bottom of the roof. This wall ties all the horizontal and vertical foundation components together.
As can be seen in this shot from the east side of the riser, the tee ties these three runs of 6" ADS double wall, non-perforated pipe to the 12" riser (the pipe was lightly perforated to facilitate condensate drainage).
This view is from the west side of a 12" riser. The tee was manufactured with a 12" x 12" x 12" tee, two 10" x 6" wyes, and two 8" x 6" wyes. The wyes were used to minimize pressure drop.
Because the building is four-stories, the 12" radon riser was enclosed in a 2 hour fire wall chase from the basement floor to the 4th floor ceiling. The framing for the chase can be seen around the pipe in the pictures below left and the finished chase below right. Four chases like these and the fans on the roof (as seen below center) is all that is seen of the four radon systems after installation.
Floor supports were needed for the 12" risers. Running through 4 floors, the riser weighed several hundred pounds.
Portions of the existing slab were to remain intact. In these areas, the floor was saw cut and trenched for the radon pipe (see picture, lower-left). Here, our patented tester was placed on a 4" line after the cement was repoured (see picture, lower-right). We did this to test for air flow and negative pressure across the entire slab.
This 6" run is routed down a long storage area.
This 6" run goes below-grade and through a 10" thick wall.
We had to core drill a 5" hole through a 10" thick wall. The ladder seen in the picture is 7 feet.
This is a 6" 3034 PVC riser in the crawlspace with Geotech cloth to minimize asbestos transfer.
Two 4" double wall runs join to the 6" double wall main line. Both are non perforated pipe that we drilled holes in to evenly distribute the negative pressure extension.
Here the 10 mil. plastic is seen over the 6" x 6" x 6" 3034 tee and 6" riser.
Here is a portion of the 10,000 sqft of 10 mil plastic that was laid during Phase 1 of the project. In all, 50,000 sqft of 10 mil plastic will be laid the crawlspace.
2" of CDF concrete was sprayed over the Visqueen in the crawlspace to completely encapsulate the asbestos.
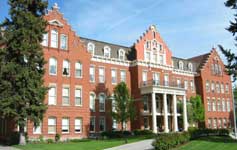
Academy Retirement Community
The Academy Retirement Community consists of two large buildings. Originally built in 1890, the Academy was known as Holy Names Academy, a boarding school for young women. The last class graduated in 1975. In 1987 the building was renovated into a retirement community.
The larger of the two buildings (above left) has two separate crawlspaces totaling 10,000 sqft separated by a 5,000 sqft basement. The crawlspaces and basement are all tied into one large system. The piping starts as 4" ADS pipe and exits the building using 10' PVC
To control the negative pressure extension in the crawlspace, we utilized solid ADS pipe (4" and 6") and drilled 1/4" holes to maximize the negative pressure extension and condensate drainage.
All of the air volume from the north crawlspace (5000 sqft) had to be piped across the basement of the structure through the foundation wall.
The basement in the main building consisted of 5 floor penetrations and extremely high air volumes. The highest air volume sump exceeded 200 cfm at 3/4" wc. (Photo at right).
The six-inch pipe (at left) carries the air from the north crawlspace. The 4" pipe was used to handle the high air volume from the 4" floor penetration. They were piped together to provide condensate drainage.
The fire sprinkler line (at right and seen below) could not be moved. The pipe slopes both directions from the sprinkler line.
This custom fitting consists of a 10" x 10" tee, two 10" x 8" reducers, two 8" x 6" tees, an 8" x 6" wye, two 8" x 6" reducers, and one 6" x 4" tee with 6" x 4" reducer.
The foundation of the facility is made up of two feet thick rock and mortar material. We used a 40 lbs jackhammer to notch the bottom of the crawlspace vent to allow the 10" duct to exit the facility below grade. We installed a 45-degree elbow as we came through the foundation to allow the duct to extend to 24 inches below grade.
The duct installed in the trench (lower left) runs to a small maintenance shed 75 feet away (lower right). Small holes were drilled in the pipe to drain condensate.
The shed footing extended greater then 24" below grade. We cut a hole in the footing and extended the pipe into the shed.
A 1½" thick PVC Flange was added to the end of the Schedule 40 12" PVC to mount the 3 hp fan. Both glue and screws were used.
Cook fan for main building
3" wc 1500 cfm 3 hp
The Assisted Living Building is 5,000 sqft and has a 4" sunken floor for the boiler. This was the only location to install the sub slab depressurization system.
Cook fan for Assisted Living Building
3" wc 650 cfm 2 hp
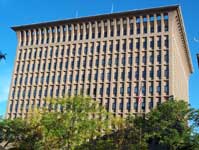
U.S. Courthouse and U.S. Post Office
The U.S. Courthouse was our most interesting radon mitigation project. This structure is nine stories in height. The sub basement is beneath the below grade parking garage, leaving the sub basement slab over 20' below grade. With the parking garage directly over the sub basement and the exhaust requirements of a parking facility, this situation created substantial negative pressure in the structure. The pressure differential between the sub basement and the sub slab environment were over 1/3" w.c. The normal stack effect of a nine story structure would be approximately .050" w.c. The amount of negative pressure in this particular structure is almost never encountered under normal conditions. Several methods for radon reduction were utilized to reduce the radon constrictions in the sub basement.
Active soil depressurization Repair of several HVAC Systems Sub basement pressurization
Step 1: The sub slab depressurization system has eighteen floor penetrations and long duct runs. The numerous existing systems (HVAC, Steam, Plumbing, Electrical etc.) made routing of the radon system complex. We decided to run the radon mitigation system through the steam tunnel into the U.S. Post Office instead of up through the nine stories of the courthouse.
Step 2: The complete HVAC control system was upgraded at the same time as the installation of the mitigation system. This repaired several defects in the HVAC system that affected the radon levels in the sub basement. For example, the parking garage exhaust fan (44,000 cfm) was running continuously with no make up air. Even small bathroom exhaust fans running continuously will elevate radon levels. One can imagine what a large parking garage fan can do.
Step 3: Sub basement pressurization was used to reduce the radon levels even further. The chiller room has two cabinet exhaust fans (4500 cfm and 6500 cfm) to remove heat. We rebuilt one of the fans and turned it around to pressurize the chiller room instead of depressurize it. The amount of air remained constant, but at a positive pressure not a negative one.
U.S. Post Office The U.S. Post Office had a radon mitigation system that was designed by our parent company, Thomas J. Gerard & Associates, Inc., and installed by the HVAC contractor during a complete remodel several years earlier.
Knowing the capabilities of the U.S. Post Office system we tied the two radon systems together and changed the fan from a 2 horsepower belt driven roof top blower to a 5 horsepower belt driven inline blower. The combined systems have 48 floor penetrations and approximately one city block of slab area. This is one of the largest radon mitigation systems in the U.S.
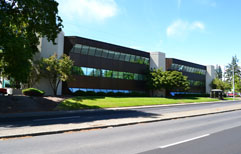
Large and Complex
Advanced Radon Technologies and designed and installed some of the largest and complex radon mitigation systems in the world. The unique geology of the Greater Spokane area makes commercial structures more susceptible not only to elevated levels or radon but in many cases very high levels (50-100 pCi/L) ART has experience in many large building ranging form very large(over 100,000 Sqft of slab/crawl space) to several high rise structures and every type of building in between. Building over 100 years old to one's just completed. ART understands how the HVAC systems and their controls have a major impact on the intrusion of radon into the structure. With our advanced diagnostic testing machine ART can design and install the most effective radon system in any type of complicated structure and do it right the first time every time!!
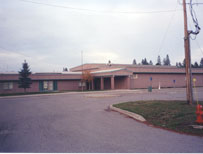
Schools
Schools present a new list of situations that are not often found in residential structures. First the occupancy is different than most commercial buildings and even the air exchange rates may vary from typical commercial structures. Advanced Radon Technologies has the expectance to assess the radon issues and mechanical system influence. ART has seen the impact of mechanical systems on radon levels during the occupied and unoccupied cycles. Swings of over 200 pCi/L were found in one local school prior to ART's installation of a complex radon system with direct interface with the mechanical controls to only run opposite of the mechanical system, saving the school district hundreds of dollars in operational and replacement costs.
Below are some examples of schools ART as installed radon mitigation systems in:
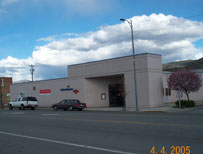
Smaller Commercial
Commercial structures of all sizes can develop radon problems. They may not have the complexities of a much larger structure, but may present issues that are not found in residential or apartment buildings. Advanced Radon Technologies has many years of experience in designing and installing radon systems in all types of commercial structures.
Below are some examples of smaller commercial buildings that ART has installed radon mitigation systems in:
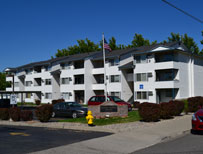
Smaller Apartments
Advanced Radon Technologies has installed radon systems in many apartment complexes all over the Pacific Northwest. From several in the Portland and Seattle areas too few in Montana and Central Washington to hundreds all over the Inland Northwest . In all ART has mitigated over 400 apartment buildings from single story to 4 stories high including a converted 4 story elementary school, built in 1904! ART prefers to install the radon systems inside the structures whenever possible following all building/Fire codes. ART believes that this is a cleaner installation and often leads to smaller more energy efficiency systems hidden in closets or storage areas.
Here are some pictures for the Smaller Commercial and Apartments page.
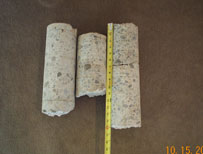